In recent years, consumer shopping habits have directly influenced the built environment; none more extreme than the increase in online purchases caused by the coronavirus pandemic. In the past 12 months, adoption of online retail has only accelerated, putting even more pressure on the sector.
While the pandemic has forced the logistics sector to adapt and innovate, it has also highlighted vulnerability. For example, the virus has led to greater absenteeism, reducing workforce availability. This has only exacerbated the labour shortages that warehouse operators were already facing. In e-fulfilment, where operations are significantly more labour intensive, finding skilled labour has become the number one priority. These skill shortages highlight the need to find a way of complementing the current work force while increasing productivity.
In addition to labour shortages, the growth of the logistics real estate sector has highlighted a lack of well-located space. E-fulfilment requires three times more storage than brick and mortar retail, with a focus on delivering goods to customers as efficiently as possible. This means increased demand for space in locations close to the end-consumer.
In Europe, one major factor driving demand for warehousing is supply chain modernisation. Occupied stock has outpaced economic growth by more than 600% in the last decade. Trends such as adoption of modern logistics real estate, urbanisation, changing demographics, and e-commerce, have piqued demand but have also put pressure on securing last-mile distribution centres.
Automation has the power to revolutionise operations, expand capabilities, improve sustainability, and increase cost efficiency in warehousing operations. When done well, automated sites are more productive, run more smoothly, have faster processing times, and are safer for workers. Therefore, it comes as no surprise that logistics customers adopting new technology have already begun to benefit greatly, experiencing greater returns on investment (ROI), sooner that they might have in non-automated settings.
The fastest-growing automation solutions are more flexible, more mobile, and less tied to physical building characteristics than they were in the past, however, it’s important for business owners and key decision-makers to understand the importance of the building itself and the role it has to play in supporting new technology. While most modern warehouses are built to a set standard, there is an increased focus on ensuring warehouse floors are flat and on a single level, to ensure easy implementation of technology. Integration with automation systems is also becoming simpler, with fixed machinery being designed for modularity, and mobile automation being introduced alongside humans. Technology can be introduced incrementally to improve existing processes, rather than supersede them – again, the focus is on labour productivity enhancement and not cold, fully-autonomous operations, or dramatic changes to real estate use.
A common myth is that automation will replace people and steal jobs, however, it has been proven to help facilitate growth, from both a human and a non-human perspective. Rather than replacing talent in the warehouse, automated systems are increasing the need for skilled workers to install, maintain, and work alongside these systems. Recent research from Prologis shows that demand for skills in areas such as data management and analysis, as well as developing training algorithms for use in optimising shift patterns or inventory management, has increased significantly. This growing demand is helping to drive up pay in the sector and create more attractive career opportunities for workers with digital and managerial skills.
The role of ‘cobots’ in the workplace has also been found to increase the productivity of workers and boost outputs, meaning businesses can meet growing demand in their current building, rather than being forced to relocate. By implementing technology such as vertical carousel storage and picking systems to collect and transport goods, the cubic capacity of the building can be maximised; for example, goods can be stored from floor to ceiling where they will be selected by a machine. This is particularly important in locations where space is at a premium.
With London’s population expected to grow to almost 10 million in 2030, demand for last-mile logistics facilities – where shipments are delivered to a transportation hub from where they make a short journey to their final destination – will only increase. By placing goods as close as possible to the end consumer, urban fulfilment centres can speed up delivery and reducing overall cost. However, the nature of last-mile logistics means that warehouse space is limited. With e-commerce operations employing more than three employees per 1,000 sq ft, adopting one or several forms of automation can help relieve some of this pressure. Reduce congestion in the facility, can also go some way towards improving the safety and wellbeing of workers.
The adoption of automation continues to grow, with pockets of growth in rapidly changing segments such as e-fulfilment and in fast-moving areas such as London. There’s no doubt about it, automation is helping supply chains move more quickly into the future, enabling dynamic, productive and well-located logistics facilities to continue serving the communities that need them.
By Eva van der Pluijm-Kok, automation specialist and research manager at Prologis
Read our 2 articles below to find out more:
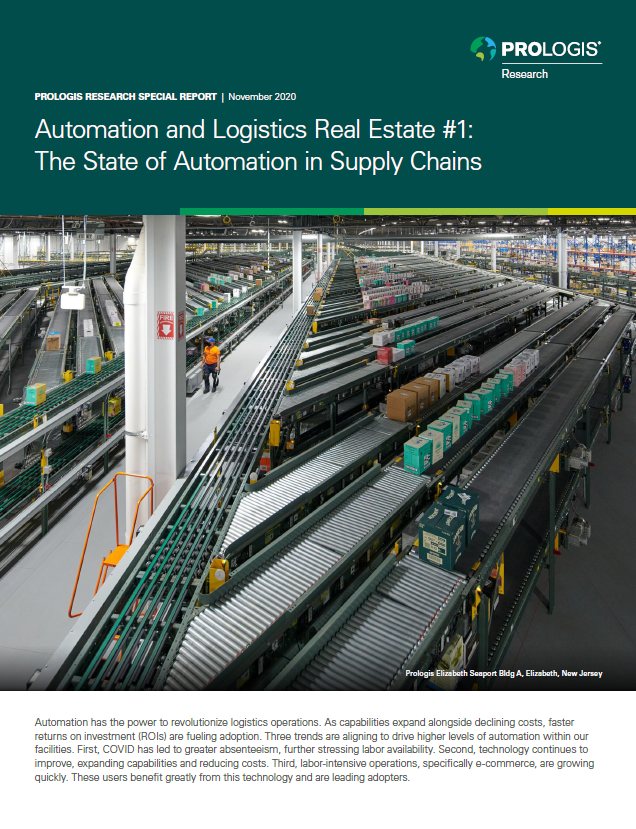
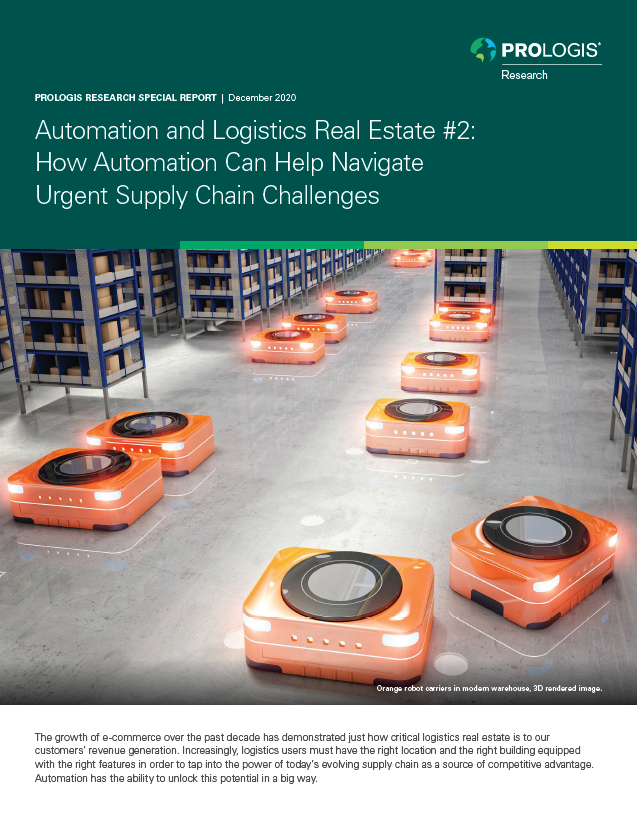